Did you know that up to 70% of concrete deterioration can be caused by freeze-thaw cycles, heavy loads, or ground settling? This surprising fact highlights the importance of recognizing when your concrete surface needs immediate attention. Ignoring early signs can lead to costly and dangerous repairs later.
Cracks, water damage, or discoloration are often the first indicators of larger problems. These issues can worsen over time, especially when exposed to varying temperatures and weather conditions. For example, a small crack in your patio or garage floor can widen, compromising the strength of the slab.
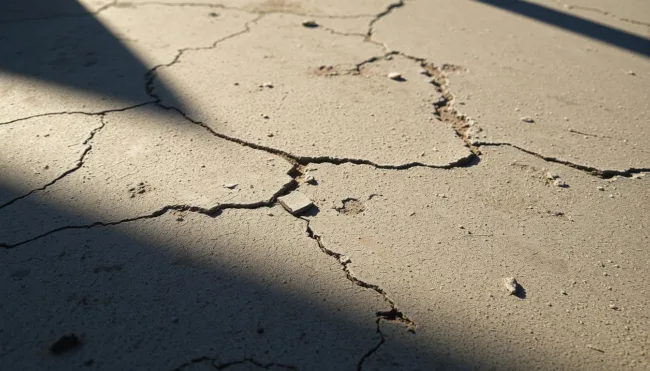
Understanding the finish and materials used in your concrete can help diagnose the root cause of the damage. Whether it’s a decorative installation or a functional area, early detection and proper maintenance can save you time and money. Stay tuned to learn more about identifying and addressing these issues effectively.
Recognizing Key Warning Signs in Your Concrete Surface
Spotting early damage can save you from costly repairs down the line. A close visual inspection is your first step in identifying issues before they escalate. Look for cracks, discoloration, or uneven areas that might indicate deeper problems.
Identifying Visible Cracks and Surface Damage
Cracks come in various forms, each signaling different issues. Hairline cracks might seem minor but can expand over time. Structural cracks, often wider or angled, suggest foundational shifts. Joint-related cracks occur where sections meet, often due to wear or movement.
Spotting Water Damage and Temperature Effects
Water infiltration can weaken the slab, leading to efflorescence or rust stains. Fluctuating temperatures cause expansion and contraction, resulting in cracks or spalling. Regular inspections after storms can help catch these issues early.
Understanding Signs of Joint and Material Deterioration
Worn joints or broken aggregate are clear indicators of material wear. Decorative finishes may show distress, such as peeling or chipping. Comparing sections of your slab can reveal uneven wear patterns.
Sign | Possible Cause | Action |
Hairline cracks | Minor shrinkage or settling | Monitor for expansion |
Efflorescence | Water infiltration | Seal the surface |
Worn joints | Material deterioration | Repair or replace joints |
Being proactive in monitoring these signs can help maintain the strength and appearance of your slab. Regular inspections and timely repairs are key to avoiding larger issues.
Practical Techniques for Diagnosing Concrete Problems
Accurate diagnosis is the first step in addressing potential issues effectively. By using the right methods and tools, you can identify problems early and take action before they escalate. Let’s explore some practical techniques to assess the health of your slab.
Conducting Visual and Tactile Inspections
Start with a thorough visual inspection. Look for cracks, discoloration, or uneven areas. Use your hands to feel for roughness or soft spots that might indicate deeper issues. For example, a rough texture could signal wear, while soft spots might point to water damage.
Pay attention to the finish of your slab. Peeling or chipping often reveals underlying problems. Regular inspections after heavy rain or temperature changes can help catch issues early.
Utilizing Comparative Tools for Surface Profiling
Specialized tools like molded rubber comparators can quantify surface roughness. These tools help you compare your slab’s texture to industry standards. Abrasive blasting and grinding are also effective methods for preparing and diagnosing surfaces.
Floor grinders and hand-held tools can detect microcracking or inconsistencies. For vertical surfaces, use tools designed for detailed inspections. These methods ensure you get a clear picture of the slab’s condition.
To assess the quality of a repair, consider adhesion tests like the pull-off method. This technique measures the strength of the bond between the repair material and the existing slab. Following industry standards, such as those from the ICRI, ensures accurate and reliable results.
By combining these techniques, you can diagnose problems effectively and take the right steps to maintain your slab’s durability and appearance.
DIY Repair Solutions and Preventative Measures
With the right tools and products, you can tackle repairs yourself. Addressing minor issues early can save you from costly replacements later. Whether it’s a crack or uneven wear, simple DIY methods can restore your slab’s durability and appearance.
Choosing the Right Tools for Surface Grinding and Repair
Surface grinders are essential for removing damaged layers and smoothing the slab. Hand-held tools can handle smaller areas, while floor grinders are ideal for larger spaces. Always wear protective gear and follow safety guidelines when using these tools.
For vertical surfaces, consider using a grinder with adjustable settings. This ensures precision and reduces the risk of over-grinding. Proper preparation, like cleaning the area, ensures better results and longer-lasting repairs.
Selecting Sealants and Repair Products for Longevity
Quality sealants protect your slab from water damage and wear. Look for products designed for your specific needs, such as those resistant to freeze-thaw cycles. Applying sealant every 2-3 years can significantly extend the life of your slab.
Repair products like epoxy fillers are ideal for cracks and joints. They bond well with the existing material and provide a durable finish. Always follow the manufacturer’s instructions for the best results.
Repairing your slab is often more cost-effective than replacing it. With the right tools and products, you can maintain its strength and appearance for years to come. Take action now to avoid bigger problems later.
Exploring Alternative Finishing and Enhancement Options
Modern advancements in finishing techniques offer endless possibilities for customization. Whether you’re working on a driveway, patio, or interior floor, the right method can elevate both the aesthetic and functionality of your space. Let’s dive into the options available to help you make an informed decision.
Comparing Traditional Finishes with Decorative Methods
Traditional methods like troweling and broom finishes are tried-and-true. Troweling creates a smooth, dense surface ideal for high-traffic areas. Broom finishes, on the other hand, provide excellent slip resistance, making them perfect for outdoor spaces.
Decorative techniques like stamped and stenciled patterns offer a cost-effective way to mimic natural materials. These methods allow for unique designs, from brick-like textures to intricate patterns. Stained finishes add color, ranging from subtle earth tones to vibrant hues.
Evaluating Precast and Advanced GFRC Applications
Precast elements are manufactured off-site, ensuring consistent quality and strength. They’re ideal for projects requiring precise dimensions or intricate designs. Glass Fiber Reinforced Concrete (GFRC) is a lightweight yet durable option, perfect for decorative panels and architectural features.
Both precast and GFRC offer faster installation times and reduced on-site labor. They’re also highly resistant to temperature fluctuations, making them suitable for various climates.
Integrating Modern Techniques with Classic Methods
Combining modern innovations with traditional practices can yield stunning results. For example, polished concrete offers a glossy, low-maintenance finish that’s perfect for commercial spaces. Exposed aggregate finishes reveal natural stones, adding texture and visual interest.
Color integration is another way to enhance your project. Integral coloring mixes pigments directly into the cement, while surface coloring applies tints after pouring. Both methods provide long-lasting, fade-resistant results.
Finish Type | Best Use | Durability |
Stamped | Patios, Walkways | High |
Polished | Commercial Floors | Very High |
Exposed Aggregate | Driveways, Pool Decks | High |
By exploring these options, you can find the perfect finish to match your needs. Whether you prefer classic simplicity or modern flair, there’s a solution for every project.
If you notice uneven surfaces or sunken concrete slabs around your property, concrete lifting can be a cost-effective solution to restore stability and prevent further damage.
Conclusion
Taking care of your slab starts with regular inspections. Early detection of cracks, discoloration, or uneven areas can prevent costly repairs. By using the right diagnostic methods, you can identify issues before they worsen.
DIY solutions like sealing cracks or applying protective coatings are effective for minor problems. These steps not only save money but also extend the life of your slab. For more complex issues, professional help ensures long-lasting results.
Consider alternative finishes like polished or exposed aggregate for added durability and style. Proper preparation and adherence to industry standards are key to achieving a strong bond and lasting performance.
Proactive care is the best way to maintain your slab’s strength and appearance. Start today to ensure it remains in top condition for years to come. For more tips or professional assistance, explore trusted resources or consult an expert.