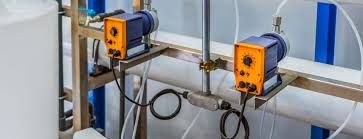
In the world of industrial applications, accuracy is not just important; it is paramount. A myriad of industries rely on the precise administration of liquids or gases to ensure quality control and maintain efficient processes. This is where dosing pumps come into play, as the cornerstone of precision in fluid handling and distribution. In this comprehensive guide, we will delve into the specifics of how these pumps function, their significance in various industrial settings, and the factors to consider when integrating them into your systems.
Understanding Dosing Pumps
Dosing pumps, also known as metering pumps, are specifically designed to deliver controlled volumes of a substance at exact intervals. These pumps are engineered to provide consistent and accurate flow rates, which is a critical requirement for processes like chemical reactions, where the exact proportion of reagents can determine the quality of the end product. The ability of dosing pumps to manage varying viscosities, pressures, and chemical compositions makes them incredibly versatile and indispensable in numerous sectors.
Key Applications of Dosing Pumps
The use of dosing pumps spans across a gamut of industries. In water treatment facilities, they play a key role in the precise addition of disinfectants or pH-regulating chemicals. The pharmaceutical industry relies on them for the careful introduction of active ingredients in drug formulations. Even in the agricultural sector, dosing pumps ensure the proper mixing of nutrients and pesticides with water for irrigation systems.
The Mechanisms Behind Dosing Pumps
To understand the operating principles of dosing pumps, it is essential to recognise the various types available. Diaphragm pumps, for instance, rely on a reciprocating diaphragm to move the liquid in and out of a chamber, providing a steady flow. Peristaltic pumps, on the other hand, utilise a rotating set of rollers which compress a flexible tube to move the contents within. Despite the differences in their mechanisms, what remains consistent is their ability to deliver precise quantities of liquid with each operation cycle.
Selecting the Right Dosing Pump
Choosing the appropriate dosing pump for your operation requires careful consideration of several factors. The chemical compatibility of the pump materials with the liquids being processed is crucial to avoid corrosion or degradation. Flow rate demands, pressure requirements, and the precision needed for your application must also be deliberated. Finally, the control features offered by the pump, such as manual or automatic operation and the ability to integrate with other systems, should align with your process needs.
Advantages of Using Dosing Pumps
The primary advantage of using dosing pumps in industrial applications is the level of control they afford. Employing dosing pumps leads to increased process reliability and repeatability, which translates to higher quality products and reduced waste. Environmental compliance is another significant benefit, as dosing pumps can aid in the accurate administration of hazardous substances, limiting the risk of spills and exposure.
Maintenance and Upkeep
For dosing pumps to function optimally, regular maintenance is critical. This includes periodic calibration to ensure accuracy, inspection of wearable parts like diaphragms or tubes for signs of wear, and prompt replacement as necessary. Cleaning and flushing procedures should also be part of the maintenance routine, especially when handling reactive or sticky substances.
The Future of Dosing Technologies
As industries evolve and technological advancements are made, dosing pump technologies continue to advance as well. Innovations in pump materials and designs are emerging to handle more extreme conditions and challenging fluids. Digital integration is also becoming more prevalent, with pumps featuring sophisticated control systems that can be monitored and adjusted remotely.
Sustainability and Dosing Pumps
Sustainability is becoming an ever-important aspect of industrial operations. Dosing pumps contribute to this initiative by minimising waste and regulating the use of chemicals to what is strictly necessary. Moreover, modern pump designs are becoming increasingly energy-efficient, producing less environmental impact while maintaining performance.
Conclusion
Dosing pumps are a silent yet essential ally in the quest for precision in industrial processes. Their role in maintaining product quality, environmental standards, and process efficiency cannot be understated. As you consider implementing dosing pumps into your workflow, it is crucial to understand the types available, the applications they suit best, and the maintenance they require. An informed approach to selecting and operating dosing pumps will undoubtedly lead to the desired outcomes in efficiency and precision.
Choosing the Right Partner for Your Pumping Needs
When integrating dosing pumps into an industrial system, the selection of a reliable partner is as important as the technology itself. A knowledgeable supplier can provide invaluable guidance on the pump types, materials, and configurations that best suit your specific requirements. Furthermore, a partnership with a proven provider ensures access to comprehensive support, from installation to ongoing maintenance and repair.
In summary, dosing pumps are instrumental in a plethora of industries where precision dosing and fluid control are necessary for success. The ability to consistently deliver exact volumes of chemicals or other substances is a function that enhances quality control, improves safety, and can even provide environmental benefits. By paying careful attention to pump selection, operation, and maintenance, organisations can optimise their processes and pave the way for a future where precision and sustainability go hand in hand.