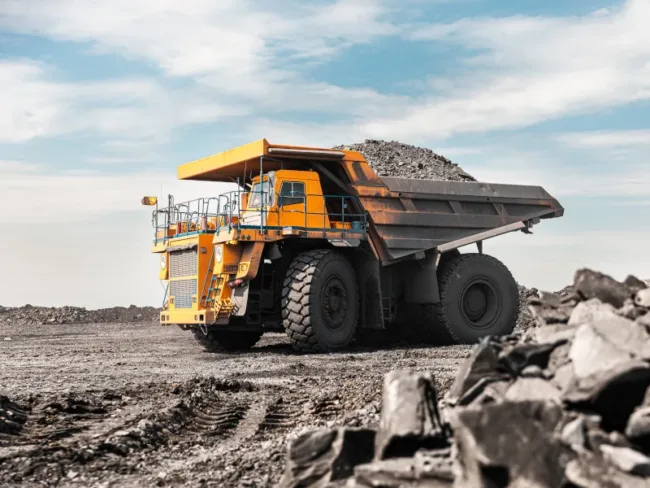
In sectors like manufacturing, construction, agriculture, and waste management, bulk material handling is more than a daily task—it’s a critical operation that impacts productivity, safety, and cost efficiency. Whether you’re moving gravel, grain, scrap metal, or chemicals, the method and tools you use can either streamline the workflow or cause serious slowdowns. This article walks you through time-tested techniques for optimizing bulk load operations, ensuring a safer and smoother process regardless of your industry.
Understanding the Challenges of Bulk Load Handling
Bulk loading deals with large volumes of loose materials, and with that scale comes a unique set of challenges. These materials are often irregular in size, heavy, and unpredictable in motion. Spills, exposure risks, equipment jams, and time loss are all common hazards. Furthermore, safety concerns arise from airborne dust, worker fatigue, and improperly secured loads.
Operators and managers need to understand these pain points not only to avoid accidents but also to identify opportunities for improved efficiency. Reducing material waste and wear on equipment directly contributes to a company’s bottom line.
Choose the Right Equipment for the Job
Not all bulk loading tools are created equal. The key to optimizing your process starts with matching the equipment to your material type and load volume. Some of the most commonly used tools include:
- Conveyor belts for continuous flow operations.
- Loaders and skid steers for mobile, flexible handling.
- Hoppers for collecting and directing flow.
- Cranes or hoists for vertical lifts.
Among these, bottom dump hoppers stand out as highly effective for controlled discharge of bulk materials. They’re particularly valuable in industries where safety, dust control, and speed are paramount. Their design enables precise unloading, minimizing spillage and exposure, while also reducing time spent on repositioning loads.
Standardize and Automate Where Possible
Automation doesn’t mean replacing human labor—it means amplifying it. By automating repetitive or high-risk steps in the loading process, you minimize human error, reduce downtime, and protect worker health.
Here are a few ways automation can help:
- Automated gates on hoppers that release materials on a schedule.
- Sensor-triggered conveyor systems that adjust speeds based on load weight.
- Integrated control panels to monitor flow rate and operational status in real time.
This kind of streamlining allows teams to focus on oversight and problem-solving rather than physically intensive tasks. According to a report from McKinsey & Company, automation in handling systems can increase operational efficiency by up to 30% in construction sectors—a benefit that translates across industries.
Implement Preventative Maintenance Protocols
Waiting for equipment to fail is a costly mistake. Unscheduled downtime often results in stalled operations, idle workers, and expensive emergency repairs. Preventative maintenance involves inspecting and servicing machinery at regular intervals to catch small issues before they become big ones.
Key steps include:
- Lubricating moving parts frequently.
- Replacing worn-out seals and joints.
- Cleaning out hoppers and chutes to prevent material buildup.
- Keeping detailed maintenance logs for each piece of equipment.
These small, routine actions can extend equipment life by years and significantly cut repair costs.
Train Staff on Load-Specific Protocols
While some handling principles are universal, the nuances of each bulk material demand custom strategies. Handling gravel requires different techniques than powdered chemicals or plastic pellets. Training your team to understand the behaviors of specific materials ensures better performance and fewer accidents.
Training should cover:
- Load distribution techniques.
- Appropriate PPE (personal protective equipment).
- Emergency shut-off procedures.
- Safe operating ranges for each tool.
Don’t overlook this step—well-trained staff can spot and prevent issues before they escalate.
Improve Site Layout and Traffic Flow
An efficient layout can dramatically reduce travel time and risks on site. Consider how your materials move from point A to point B. Are there unnecessary detours? Are machines crossing paths with workers or other machines?
To optimize the flow:
- Designate one-way paths for heavy machinery.
- Use color-coded floor markings for pedestrian zones.
- Position key equipment near staging areas to limit transport distance.
Well-organized layouts also contribute to faster response times during emergencies.
Monitor Load Weights and Discharge Rates
Overloading or underloading equipment leads to uneven wear, wasted fuel, and structural stress. Installing weight sensors on hoppers, trucks, and conveyors ensures you’re moving optimal amounts with each cycle. Likewise, monitoring discharge rates can help you fine-tune flow speed for maximum throughput.
Modern digital scales and load cells can transmit data directly to your operation dashboard, allowing for instant adjustments and performance analysis.
Encourage a Culture of Continuous Improvement
Operations don’t improve by chance—they improve through deliberate effort and adaptation. Involve your team in identifying bottlenecks, offering suggestions, and testing new methods. Hold regular debriefs and use real data to inform future changes.
Additionally, implement feedback loops where operators can report inefficiencies without fear of blame. Often, the most useful insights come from the people closest to the process.
Final Thoughts
Bulk load operations may seem routine, but when optimized properly, they offer a significant competitive edge. By selecting the right equipment, prioritizing safety, and investing in smart workflows, any business can turn a logistical headache into a well-oiled system. Whether you’re managing bottom dump hoppers or designing automated conveyor lines, it all comes down to strategic planning and ongoing refinement.
Optimizing bulk load handling isn’t about chasing perfection—it’s about making every part of the process safer, smarter, and more productive.